RADIOSS在抽钉铆钉连接振动疲劳对比试验中的应用
Application of RADIOSS in The Draw Rivet & Rivet Vibration Fatigue Experimental
梁飞 刘秋娥
(中航工业西安飞机工业公司陕西西安710089)
摘 要:基于Altair公司HyperWorks软件平台,采用HyperMesh软件建立了某型飞机进气道抽钉铆钉振动疲劳试验件的有限元模型,并用RADIOSS求解器对振动试验件进行了模态分析,为试验中T字型悬臂板结构试验件出现的圆角区裂纹问题提供了理论依据,并为试验方案的改进提供了指导。
关键词:HyperWorks RADIOSS 振动疲劳 模态分析
Abstract: Based on the HyperWorks software platform, this article tests a finite element model of the air inlet draw rivet & rivet vibration fatigue experiment that has been established with HyperMesh. The modal analysis was performed by RADIOSS solver. The cracking problem of fillet area T type cantilever structural test part provides a theoretical basis and guidance for the improvement of test programs.
Key words: HyperWorks, RADIOSS, vibration fatigue, modal analysis
1 概述
在航空领域,飞机结构的振动疲劳问题是广泛存在的。而目前我国对振动疲劳问题的研究还处于初步阶段,基础比较薄弱,对结构振动疲劳的机理没有准确统一的认识,也没有建立起一套系统的试验方法。某型飞机进气道常出现的蒙皮裂纹、铆钉松动以及掉铆钉头等故障即为典型的振动疲劳问题。
某型飞机进气道由前转接气道、上管道、下管道以及后转接气道组成,外场飞机出现以上故障时,由于故障部位铆接环境差,维修人员无法接近,给维修带来了很大难度,进而造成进行拆卸维修耗时太长并直接影响到飞行任务。因此,外场中需使用抽钉连接铝质加强片的方法实现快速维修。为了验证此种方法的可靠性,有必要进行进气道抽钉铆钉连接振动疲劳对比试验。
试验件的结构设计是振动疲劳试验的关键因素,其方案的优劣会直接影响到能否得到科学客观的试验结果。某型飞机进气道抽钉铆钉连接振动疲劳对比试验件设计的关键问题在于能否使试验件疲劳部位恰好发生在所需考核的部位。试验前期,根据现有的资料与经验,将试验件设计成T字型悬臂板结构形式,所带来的问题是试验中设计考核部位出现疲劳的概率要远小于T字型悬臂板圆角过渡区部位。所以有必要对试验件的结构形式进行进一步的优化,保证疲劳部位应先发生在所需考核的部位。
本文中采用RADIOSS模态分析模块分析了T字型悬臂板试验件的振动特性,并与试验结果进行了对比分析,为此种结构在试验中存在的圆角区首先疲劳的问题作出了解释,进而对试验件结构形式进行了优化,得到了一种能够满足试验要求的试验件结构形式。
借鉴现有研究资料中振动疲劳试验件的结构形式,选择单端夹持方法进行抽钉铆钉振动疲劳摸底试验。试验件由加强板(LY12-CZ-δ1.2)、蒙皮(LY12-CZ-δ1)和材料为LY12的型材用铆钉(或抽钉)铆接在一起,具体结构形式如图1所示。其中考核部位位于角材上,由2个3.5mm、90°埋头铆钉与2个牌号为CR3252-4-03的100°沉头抽钉组成,其中铆钉与抽钉交错排列。试验件与夹具的安装如图2所示,夹持长度为60mm。
2.2 试验方法
由于没有某型飞机进气道实际测定的振动疲劳载荷谱,故采用共振疲劳试验方法进行试验。试验在DC-3200-36振动台上进行,分别采用CA-YD-107CM加速度传感器与4344S压电加速度计进行振动的控制与监测。在试验件上的考核部位粘贴应变花,并用DH5927信号采集设备进行应变数据采集分析。应变花粘贴位置如图3所示。
分别采用6组试验件的一阶频率,利用谐波驻留方法进行激励共振,恒定加速度为5mm或为4mm。试验中,当共振频率减小5%或者监测点振幅发生明显变化时认为试验件疲劳失效。
图1 T字型悬臂板结构试验件 图2试验件与夹具的安装
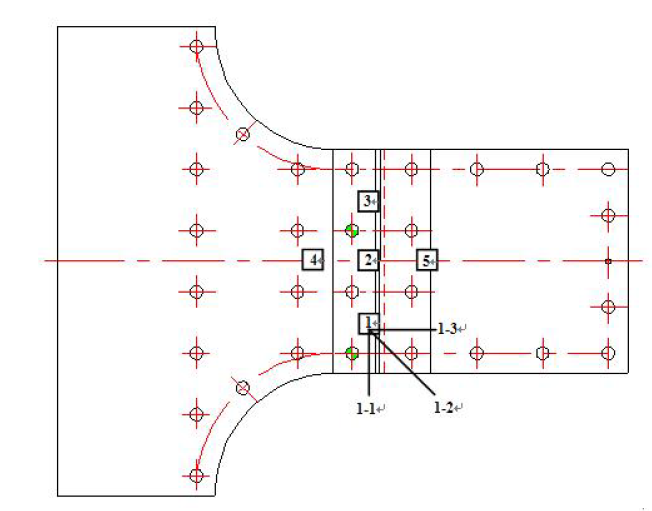
图3 应变花粘贴位置
2.3试验结果
试验数据如表1所示。从中可以看出,6件试验件中有5件圆角区均出现了裂纹,只有三件疲劳破坏(掉铆钉头现象)出现在考核部位,故此种结构形式试验件结果并不满足疲劳应先发生在考核部位的试验要求。
表1 前期摸底试验数据
图 4 圆角过渡区裂纹 图5 铆钉头脱落
3 有限元模态分析与试验方案改进
3.1模型的建立
按摸底试验试验件结构形式建立有限元模型,蒙皮、加强板与角材均采用二维壳单元QUAD4,其相互之间采用RBE2单元模拟铆钉和抽钉进行连接,如图6所示。
蒙皮、加强板与角材的材料均为LY12-CZ,弹性模量E=70GPa,密度为2800Kg/m3。
约束蒙皮和加强板靠夹持端60mm内单元6个自由度,即为单端夹持振动试验的边界条件。
在RADIOSS Bulk Data模块中采用normal modes对建立好的模型进行模态分析。
图6 有限元模型
3.2结果分析与方案改进
3.2.1 振动特性分析
图7与图8分别是试验件在一阶模态下的相对应力与相对位移云图,虽然位移与应力值都不是真实的,但是相互比较仍然可以说明此结构振动时的一些特性。图7中可看出一阶共振频率为33.25HZ,与试验中结果相吻合。
经验表明,与静疲劳类似,结构的应力水平是决定振动疲劳寿命的关键因素之一,应力水平大的部位要更容易出现疲劳。图7中可以看出,在一阶模态下,试验件相对应力最大的区域在圆角区与夹持段的根部,为试验中圆角区总出现裂纹提供了理论依据。
图7 相对应力云图
图8 相对位移云图
3.2.2试验件结构形式改进
为排除振动时试验件圆角区出现裂纹对试验造成的不利影响,对试验件结构形式进行了重新设计,加大了圆角半径,(图9与图10)并且利用RADIOSS对单端夹持与两端夹持振动方法分别进行模态求解,分析新结构的振动特性,为抽钉铆钉振动疲劳对比试验的最终方案提供参考。
图11可以看出,在单端夹持的情况下,圆角区的相对应力仍然最大。而图12中,两端夹持的情况下,相对应力最大的部位出现在蒙皮、加强板与角材三者连接的地方,也即本实验的考核部位。
所以,消除圆角区裂纹不仅要从优化结构入手,而且与夹持方式密切相关。从仿真结果来看,重新设计试验件结构形式后,采用两端加持的方式进行振动疲劳试验是比较合理的方案。
图9 优化后试验件单端加持 图10 优化后试验件两端加持
图11 优化后试验件单端加持相对应力云图 图12优化后试验件两端加持相对应力云图
3.3 RADIOSS在试验方案改进中的作用
RADIOSS的模态分析是其分析应用中最基本的一项功能,但是在本试验方案的改进中起到了关键的作用。模态分析结果不仅为试验中出现的问题提供了理论依据,同时也很好的指导了试验件结构形式与试验方法的改进。如果在摸底试验方案起草的初期使用RADIOSS模态分析介入设计,便可以以较小的代价、较短的时间内完成设计方案反复迭代的过程,缩短试验时间、大幅节省试验成本。
4 总结
(1) 前期摸底试验中出现的试验件圆角区裂纹问题是由于试验件结构形式与夹持方式不当引起的;
(2) 试验件结构形式经重新设计并采用两端加持方式后能避免试验件圆角区出现裂纹的问题;
(3) RADIOSS在本试验方案改进中的应用大幅缩短了试验时间、节省了试验成本,为以后类似试验件结构方案的设计提供了一个优秀的模板。
5 参考文献
[1] RADIOSS User’s Manual
[2] 徐志刚,陈荣,李权,姚起杭.某型飞机进气道在噪声环境中的振动疲劳分析[J]. 装备环境工程, 2011
[3] 张钊,张万玉,胡亚琪.飞机结构振动疲劳分析研究进展[J]. 航空计算技术, 2012
如有业务的需要请联系电话:13723451508,咨询QQ:215370757
本文出自深圳有限元科技有限公司 cae软件专业网站:http://www.feaworks.org 转载请注明
|