摘 要: 本文阐述在某款SUV项目研发的过程中,利用Altair OptiStruct解算器成功完成了NVH-CAE相关的工作,从零部件、子系统到车身、底盘和整车,从目标设定、目标分解到性能优化,初步建立起了汽车振动噪声NVH-CAE的研发流程与平台。利用AMSES加速模块在保证精度的前提下,非常显著地缩短了每轮NVH计算的求解时间,为本次项目工作带来了非常大的帮助。
关键词: 整车NVH NVH-CAE OptiStruct AMSES
Abstract: In the process of SUV project development, Altair OptiStruct solver performed all of the NVH work successfully, from components, subsystem to body, chassis and full-vehicle, from target setting, target decomposition to performance optimization, built the process and platform of vehicle NVH. And with the OptiStruct AMSES acceleration module, the time of NVH analysis each round reduced effectively while analytical precision were reliable. Altair OptiStruct and AMSES can provide efficient help for this project.
Key Words: Full-vehicle NVH, NVH-CAE, OptiStruct, AMSES
1 概述
在评价汽车的振动与噪声时,通常从三个方面来评价:整车评价、系统评价和部件评价。整车评价是从顾客的角度出发来评价整个车噪声与振动的水准,通常包括车内评价与车外评价。车内评价指标有驾驶员和乘客耳朵感受到的声压级,方向盘、地板、座椅等关键地方的振动。车外评价指标是是政府制定的“通过噪声”。系统评价是评价一个系统的噪声与振动水平,比如排气系统,尾管的噪声要满足一定的要求。部件评价是指部件的振动与噪声达到规定的指标,如排气系统中的消声器,其指标是声音的传递损失。整车是由系统组成,系统是由部件组成,因此部件NVH的水准决定了系统NVH的水准,系统NVH的水准进而决定了整车NVH的水准。按照汽车产品的研发进程,同样也是遵从部件→系统→整车的研发顺序,虽然用户最关心的是整车的NVH性能,但是作为研发人员必须从部件性能、系统性能把控做起,从而得到一个好的整车性能。
图1 部分整车NVH分析内容
CAE与NVH的结合,即通常所说的NVH-CAE,近年来一直是国内车企研发持续关注的重点领域。CAE在前期介入NVH开发流程中,对提高整车NVH性能、减少样车整改时间,缩减成本起到很大的作用。本项目从零部件CAE做起,到子系统、车身、底盘和动力总成,再到最后的整车,为公司后续产品的NVH-CAE开发流程建立起了初步的标杆。此次整个NVH-CAE流程涉及的分析内容很多,需要攻克的技术难点也不少,除了关注CAE仿真本身的性能预测外,CAE与试验结果的比对也是需要重点考察。本文将着重介绍此次项目中关注的重点与难点问题。
广汽吉奥,作为广汽集团旗下的自主品牌,立志实现“做强皮卡、做大微面、做精SUV”的企业愿景。广汽吉奥某款目前在研车型,定位于精品城市SUV市场,整车全新设计正向开发,各主要系统设计和匹配伴随着很多技术难关,在车企新车研发周期普遍较短的环境下,CAE仿真在吉奥的研发体系中发挥着极大的作用。CAE仿真分析最重要的就是把握计算效率和精度,对于本款SUV车型,CAE仿真分析工作量大,难度系数和设计目标值要求也很高,既要保证整车的气动性能、发动机舱热保护关键区域以及除霜、除雾能力,又要评估整车安全性能是否能够达到新版C-NCAP规则(2012)五星级要求,同时,做为广汽吉奥汽车的一大卖点-----整车NVH性能,是CAE分析工作的重中之重,为保证车型的NVH性能,全新车身结构和动力系统的匹配更需做多轮次的CAE校核,整车各主要系统的模态解耦以及振动、噪声响应分析需做多轮NVH优化改进。
2 NVH仿真在产品开发中的应用
利用Altair OptiStruct解算器可以求解从零部件、子系统到车身、底盘和整车全部的NVH-CAE相关工作,特别是在HyperMesh中集成了Process Manager前处理工具,极大地改善了整车NVH分析的流程,而且在HyperView中也集成了若干NVH相关的后处理工具,从模态贡献量分析、板件贡献量分析,到节点贡献量分析、能量分析和传递路径分析(TPA),再到设计灵敏度分析与综合诊断,极大地提高了NVH后处理的效率,帮助分析人员更有效地辨识问题源头,并从后处理过程中寻找到关键的解决办法。
利用Altair OptiStruct自带的AMSES加速模块在保证精度的前提下,非常显著地缩短了每轮NVH计算的求解时间,原来整车NVH分析工况一般需用几十个小时来计算,但用AMSES可以缩短到几个小时,为本次项目工作带来了非常大的帮助。
本次新设计车型采用全承载式车身结构,全承载式车身几乎承载了车辆使用过程中的各种载荷。在这些载荷的作用下,车身的刚度特性具有举足轻重的作用。车辆车身刚度的优劣直接影响到其使用性能的正常发挥,车身刚度不合理,将直接影响车辆的NVH性能、可靠性、安全性、动力响应特性及燃油经济性等关键性能指标。因此,在新车型开发阶段,尤其是预研阶段,就需要做好指标控制。
CAE仿真结果为了与试验达到一致,必须组织专门的对标工作,对标CAE分析与试验在边界条件、加载方式、白车身状态和测量点等的一致性,保证设计数据阶段的CAE分析结果能够准确反映白车身数据的刚度情况,减少后期的整改时间。刚度CAE计算在理论上已经非常成熟,在这次项目中引入白车身刚度分析后,在样车试验阶段没有再出现白车身刚度整改的情况,车身是整车的基础,良好的基础是良好整车性能的必要条件。
2.1.2车身模态
1、车身模态是车身动力学性能最基础的性能。通过车身模态分析,其目的有:
2、检查和调试模型,及时更正模型错误,保证计算的准确性;
3、白车身的一阶扭转和一阶弯曲频率是车体刚性的重要反映,决定了汽车骨架的好坏,如果频率过低,需要通过优化车身结构来提高其固有频率。建立数据库,并与其中同平台车型进行比较和评价;
4、通过白车身、内饰车身和整车的局部模态可以找到车身结构上的薄弱环节,找到声固耦合区域,通过优化这些区域来发现车身结构上的潜在NVH隐患。
Altair OptiStruct提供了一系列优化工具,特别是灵敏度分析、尺寸优化和自由尺寸优化等分析方法,能非常有效地辨识出对模态频率影响较大的车身部件和结构区域,并且针对上述部件和区域进行优化改进后,模态频率的确提高非常显著,最终达到性能目标。
图2 白车身灵敏度分析结果
图3 白车身自由尺寸优化结果
图4 TB车身模型组成
图5 TB模态分析结果
2.1.3连接点动刚度
发动机和悬架在车身上的连接点的动刚度是影响车身NVH性能的重要指标,进行动刚度分析可以了解对车身输入激励的位置刚度情况。如果刚度不足,那么对车身形成的激励信号通过连接点后将会被放大,进而造成车身响应较大,所以有必要对底盘、动力总成与车身之间的连接点进行动刚度分析。频率响应分析可以求出结构在多种频率下的位移、速度和加速度的响应,进而得到相应的频率响应曲线。根据响应的特征又可分为:位移、速度和加速度频率响应函数三种,在车身CAE分析中,动刚度分析常采用速度导纳进行评价。
图6 TB前悬架连接点动刚度结果
图7基于动刚度分析的模态贡献量分析结果
2.1.4车身传递函数
传递函数分析是用来计算结构系统在稳态振动激励下响应的方法。通过频率响应分析,可以直观的了解系统在那些频率下容易被激起共振。通过对结构以及结构-声场耦合系统的频率响应分析,可以找出结构和车内声场在哪些频率处容易出现结构共振和声腔共鸣,从而为后面评价和结构改进提供一定的参考。
结构传递函数分析目的是考察响应点的振动水平,噪声传递函数分析目的是考察响应点的噪声水平,根据国标(GB/T4970-1996)结构传递函数分析频率范围是1~80Hz,频率分辨率为1Hz;人耳听力阈值20~20kHz,有限元低频结构声分析一般只针对200Hz以内的频率,所以噪声传递函数分析频率范围一般是20~200Hz。
图8 整车振动响应点示意图
图9 声腔模型示意图
图10 NTF优化前后对比结果
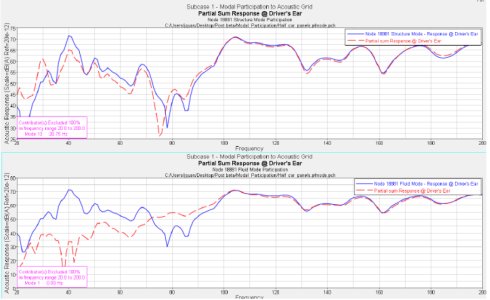
图11 基于NTF的板件贡献量分析结果
2.2底盘NVH仿真
底盘连接点的位移×底盘连接点的刚度×底盘连接点到声腔响应点的传函=乘员感知噪声
图12 利用底盘模型进行车内噪声仿真分析
第一步,建立详细的底盘有限元模型,在发动机曲轴中心点施加载荷,计算载荷通过底盘总成到达各个车身连接点的响应结果,响应结果以位移值表示。
第二步,建立底盘总成的多体动力学(MBD)模型,在MBD分析中得到底盘与车身各个连接点的刚度值。因此,底盘连接点的位移×底盘连接点的刚度=底盘连接点的传递力。
第三步,利用TB车身与乘员声腔的有限元模型,计算从底盘连接点到乘员舱内声音响应点的传递函数。这样利用第二步中计算得到的底盘连接点的力×底盘到乘员舱内响应点的传递函数(FRF)=车内乘员舱响应点的噪声响应。
2.3整车NVH仿真
利用有限元频率响应分析方法,进行车身结构振动加速度预测和控制、由壁板振动引起的车内噪声预测和控制的研究工作,在所建立的车身结构—车室空腔声场耦合系统模型上施加激励,因为车身结构的振动激励来源于发动机、传动系和路面不平度产生的振动,所以按照频率响应分析的要求,结合汽车的实际行驶工况,同时了考虑来自发动机和路面的激励力载荷。整车NVH分析能力,是车辆NVH-CAE分析的核心能力。建立一个精确的整车模型是NVH分析的重要前提,一个整车模型的精度,很大程度上取决于建模过程。整车有限元模型的建立是振动仿真分析方法在汽车上的具体应用,具有很强的实践性,不仅需要有扎实的有限元理论基础和熟练的软件使用知识,还需要对汽车构造有深入的了解和深厚的建模经验积累。同时结合整车试验的测试结果,开展CAE和试验测试的相关性分析,对建立的整车模型进行标定,使建立的整车模型精度满足要求,从而增加CAE仿真对项目支持的信心。
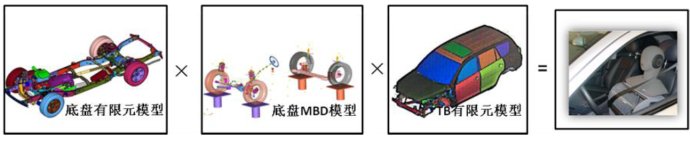
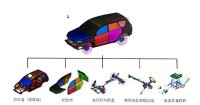
图13 整车NVH模型组成示意图 图14 整车NVH模型示意图
2.3.1整车模态分布规划
汽车上各个系统是相互连接在一起的,比如排气系统、悬架系统等与车身相连接,进排气系统与发动机相连接。为了避免产品相连系统之间发生共振,在产品开发初期,就必须考虑整车结构特征和各个系统的布置,使得相互系统间的振动影响最小。减少整车低频振动,可以从下面几个方面来考虑:
(1)避免发动机、车身和与之相连接系统之间的频率耦合。发动机的振动是与转速和阶次有关的,与发动机相 连接的部件有很多,因此要使得这些部件的固有频率避开发动机的激振频率。
(2)避免车身壁板的结构模态与乘员舱的声学模态耦合。
(3)避免悬架系统与车身上附件的模态耦合。轮胎和悬架的垂向振动模态通常与车内座椅的摆振频率接近,当 左右车轮的异步振动时,座椅的摆振模态容易被激起来,引发乘客的不舒适性。
基于以上原则,整车模态频率分布表的规划就十分必要,在概念设计阶段就对整车模态的分布进行了规划,避免整车各个系统之间出现振动耦合,从而可更好的在设计前期实现对整车NVH性能的管控。
图15 整车模态分析结果
图16 整车模态频率分布表
2.3.2基于发动机激励的整车振动、噪声分析
汽车在静止(怠速)和运动(加、减速)过程中,发动机激励是主要的外界激励源。在发动机中,确切地说是在往复活塞式发动机中,由于反复做上下运动的活塞和燃烧过程,产生了附加力和扭矩,它们通过动力总成悬置激发汽车底盘的振动。由此产生的振动和噪声将对车厢内乘员产生不舒适性。根据提供的转鼓台架试验发动机悬置和副车架的加速度信号,获得发动机悬置处的力载荷,且各个转速的倍频均在基频上可找到对应频率。
目前,主要有两种分析方法来对上述问题进行分析和优化。在设计前期,可以根据发动机本身的工作参数,通过物理公式以及数学公式的推导,得到相应的激励载荷,在发动机质心进行加载,通过对不同传动路径的分析,找到引起问题的激励路径进行优化,从而减小或消除车内的振动和噪声。在设计中、后期可以根据选用的发动机在车身中测出不同频率下的激励载荷,这时就可以在发动机悬置处进行加载。应用发动机振动噪声分析找到设计不合理的地方,主要可以从前期悬置解耦、悬置被动侧支架的结构,以及车身结构来考虑进行优化,快速找出问题原因,并与试验部门一起进行试验验证,提供整改方案,来达到对车内NVH问题整改的目的。
图17 发动机激励下的车内振动响应
图18 发动机激励下的声腔节点贡献分析结果
2.3.3基于路面激励的整车振动、噪声分析
当车辆在路面上行驶时,它经历一个宽阔的振动频谱,这些振动最终表现在方向盘、转向柱、座椅、地板以及后视镜上的振动,还有由于振动产生的车内噪声。依据噪声产生的机理不同,路面激励下的车内振动噪声可细分为结构传播噪声和空气传播声两个方面,它是一个系统的、复杂的问题,其涉及到底盘零部件结构、减震元件设计、车身结构及局部刚度相互匹配的问题。
利用多体动力学仿真技术确定出路面不平度激励对车身的力载荷,通过声固耦合作用将这些力转变为车身结构振动和车室内部的声压级,就可以评价不同工况下车身结构振动和车室内部的结构噪声。
图19 车速60km/h工况下车内噪声分析结果
图20 基于路噪的传递路径分析(TPA)结果
2.3.4轮胎不平衡力激励
对于高速旋转体,由于材料的分布不均、制造、安装等方面的误差,总存在旋转体的质心位置与转动中心位置存在偏差。轮胎在高速旋转情况下,偏心质量必然会产生交变的离心力,从而引起汽车的振动、噪声,影响车辆操纵性、舒适性和平稳性,严重的会损坏汽车零部件,甚至引发交通事故。因此,分析轮胎不平衡力的激励影响对汽车在NVH性能上有很重要的意义。
轮胎出厂时都要做动平衡试验并进行平衡校正,所以一般的轮胎,偏心质量和偏心距都很小,根据各档位传动比和主减速比等参数来计算轮胎不平衡力激励幅值和频率与发动机的转速和档位的关系。随着发动机转速与档位的升高,轮胎不平衡力的幅值和频率均呈现上升趋势。
图21轮胎不平衡分析结果
图22 基于轮胎不平衡的模态贡献量分析结果
3 总结
本次项目根据广汽吉奥汽车振动噪声自主研发的需求,工作内容从零部件、子系统到车身、底盘和整车,从目标设定、目标分解到性能优化,初步建立起了汽车振动噪声NVH-CAE的研发流程与平台。该流程与平台分为了分析体系、产品能力和关键技术几大部分,通过本次项目的成功开展,建立了一整套完整详细的NVH-CAE分析规范,并在实际项目中与设计、试验、工艺、制造等专业协同工作,为广汽吉奥汽车的自主研发提供了有力的支撑。
致谢:本文在写作过程中,得到了澳汰尔公司工程咨询部李颖琎的支持,在此表示感谢。
4 参考文献
[1] 骨正气主编 《轿车车身》 人民交通出版社 2002
[2] 庞剑等编 《汽车噪声与振动》 北京理工大学出版社 2006
[3] Joseph C. Benedyk. Light Materials in Automotive Applications[J]. Light Metal Age.2000(10): 34-35
[4] Stephen Logan, Al Kizyma。 lightweight magnesium intensive body structure. SAE Technical Paper Series 2006-01-0523
|